COST & PRODUCTIVITY DIAGNOSTIC | COMPLEX GOLD MINE
EMEA
CLIENT
Large EMEA Gold Producer
OBJECTIVE
Xenco was engaged to perform a rapid diagnostic assessment of a large gold mine in the EMEA region. The goal was to evaluate mine planning, asset management, and processing workstreams to identify inefficiencies and cost drivers, ultimately delivering strategies to enhance operational performance.
THE CHALLENGES
The mine faced significant inefficiencies across its operations, leading to production constraints and increased costs. Key challenges included:
- Inadequate long-term planning – A lack of scenario modelling and risk mitigation strategies impacted mine design and execution.
- Mining inefficiencies – Poor blasting, grade control, and stockpile management resulted in ore loss and dilution.
- Processing bottlenecks – Low milling circuit runtime and oxidation inefficiencies limited throughput.
- Reconciliation and accountability gaps – Weak production tracking led to unaccounted metal losses.
- Asset and contractor management – Inconsistent maintenance planning and contractor oversight increased costs and downtime.
APPROACH
Xenco executed a structured assessment, starting with a remote diagnostic lite analysis to identify key themes, followed by on-site validation. We then developed a targeted improvement plan, ensuring alignment between corporate objectives and daily site activities. Our approach focused on:
- Aligning corporate strategy with site-level and departmental goals.
- Identifying key cost and productivity drivers.
- Delivering practical recommendations to streamline operations.
The diagnostic focused on four key areas:
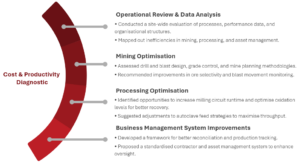
OUR RESULT
Xenco’s diagnostic uncovered substantial opportunities for cost savings and efficiency gains, including:
- >$20 million in annual cost reductions through optimised contractor management, processing strategies, and production reconciliation.
- Up to 43,000 oz per year in additional production by improving mining processes, reducing bottlenecks, and optimising processing strategies.
- 10% uplift in productivity through structured maintenance planning, enhanced contractor oversight, and better shutdown execution.
- 15.8% reduction in All-in Sustaining Cost (AISC) per ounce, improving profitability and sustainability.
- Improved planning strategies, including enhanced scenario modelling, grade control drilling, and waste movement planning for greater operational stability.
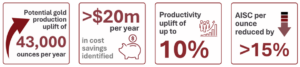