SHUTDOWN STRATEGY IMPROVEMENT
OBJECTIVE
Xenco was engaged to support a major mine to improve its complex shutdown procedures. Our primary objective focused on improving plant performance through enhanced shutdown strategies and execution effectiveness.
THE CHALLENGES
The existing system had multiple areas for improvement in shutdown strategies and procedures.
- Inadequate shutdown readiness and execution processes resulting in unpredictable schedules and execution overruns.
- Reactive shutdown execution behaviour elevated the safety risk profile exposure to lost time injuries.
- Frequent shutdowns (planned and unplanned) affect the plant’s Mean Time Between Failures (MTBF), overall plant performance, and limit the throughput.
- Inefficient reline schedules and poor planning of major events leading to increased shutdown frequencies and inefficient execution.
- Limitations in gland and process water valve layout and design restricting mill utilisation and the ability to operate major milling capacity during partial plant shutdowns.
APPROACH
We delivered a planned and predictable approach to shutdown execution that improved overall people and plant operating efficiency and ultimately increased plant performance. Our team’s key focus was:
Implementation of disciplined processes and systems
- Leading to predictable execution schedules.
- Elimination of overruns due to poor readiness.
- Providing guidance on structures, skills and significant coaching and development across all key shutdown roles.
Optimisation of reline schedules and major events planning
- Successfully reducing shutdown frequencies.
Modification to the gland and process water valve layout
- Delivering process flexibility.
- Enabling the capacity to operate major mills during partial plant shutdowns, reducing overall plant downtime.
OUR RESULT
The implementation of an improved shutdown strategy that focused on delivering a planned and predictable approach led to significant improvements across several key areas of plant performance.
“The improvements led to tangible benefits, including a significant uplift in average tonners milled per day. Within the first three months of intervention, the company experienced an increase in throughput.”
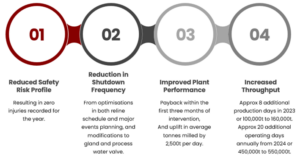
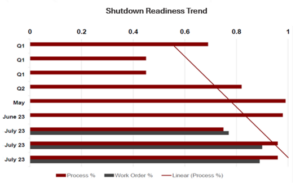
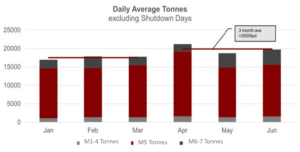